Services
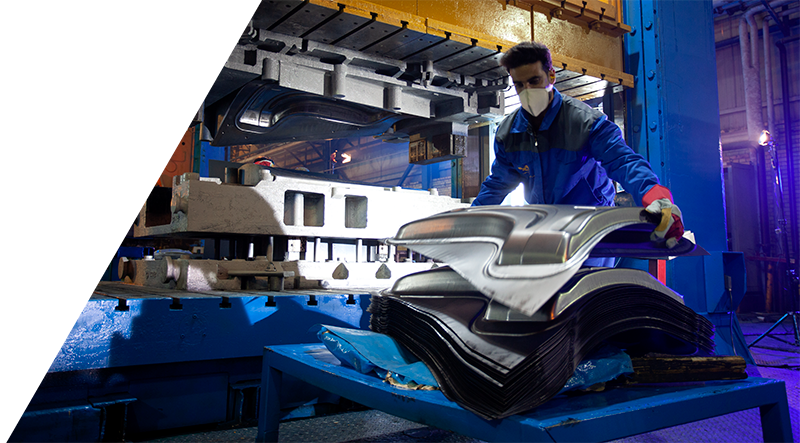
Panel Forming
Heavy Press Factory & Medium Press Factory
- Production of automotive components using state-of-the-art press machines, including mechanical and hydraulic presses
- Having Grade A quality from SAPCO company for the production of automotive components, and employing a specialized press machine for waste materials in the pressing workshop
- Production of household appliance components with the highest quality and the most experienced operators
- Production of automotive components with over two decades of manufacturing experience and the highest quality
Maintenance and repair of molds
The main task of the High Mold Maintenance Unit is to increase the efficiency percentage of the delivered molds. To achieve this, the factory must be equipped with a strong preventive maintenance team. When the molds are transferred from the production line to the maintenance unit, they all undergo a detailed inspection.
It is worth mentioning that at this stage, specialized individuals with specific expertise, including welding and tri-out machining, are utilized, as each repair may require specific skills.
Ultimately, the goal of the supervisor and the planning unit of the High Mold Maintenance is to minimize emergency repairs by conducting periodic and preventive maintenance in this unit
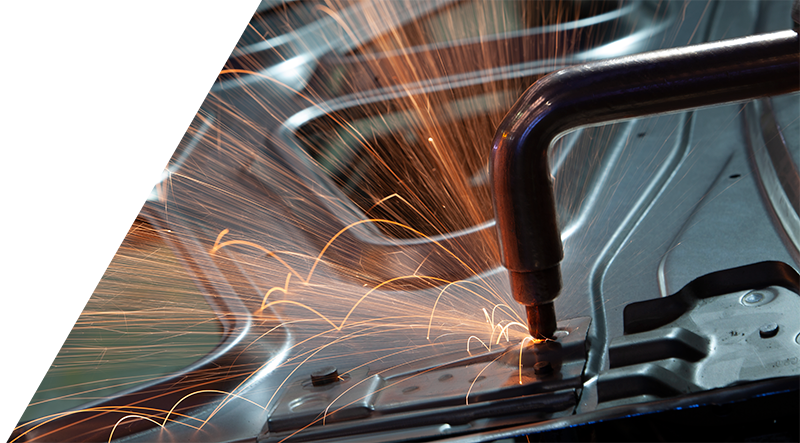
Component Manufacturing
To transform a hard and cold steel sheet into a usable component in a car, we navigate a challenging path, and we are committed to designing and directing the highest quality, cost-effective, and technological route for the production of your automotive parts.
The production process at Asia Khodro Synchronization Company takes place in ten different halls, equipped with approximately one hundred mechanical and hydraulic presses, ranging from 63 to 1250 tons, twenty-two assembly robots, three laser and plasma cutting robots, and three mechanized primer painting lines.
۱. Tool and Die Factory
In this tool and die factory, specialized steel molds for presses in sizes G1 to G5 are designed, modeled, and manufactured.
2. Sheet Metal Cutting Factory
Steel sheets are cut to the optimal size for each component based on the designs provided by the technical and engineering unit, and then transferred to the press shop
3. Pressing Operations
The cut sheets in these workshops undergo pressing and forming operations.
4. Laser and Plasma Cutting Robots
After the forming process, pressed components are transferred to this section for trimming and precise hole drilling. The advantages of laser and plasma cutting include very high speed and precision in cutting and hole drilling.
5. Welding and Hemming Assembly Robots
Automotive assemblies requiring multi-piece assembly are welded by welding robots, and the surface and double part are assembled on top of each other by hemming robots.
6. Plating
Internal body components, such as the front bumper reinforcement for Peugeot 405, undergo the galvanized plating process in this section.
7. color
There are three separate primer painting lines. Initially, the produced products are degreased and washed. Then, for the primer paint to penetrate the component, the parts are phosphated. Subsequently, they are dried in the pre-heating stage and prepared for the paint spray. After the primer painting stage, the painted components are finally transferred to the baking furnace.
8. Packaging
After all stages of painting and waxing, if necessary, the components are placed in bubble wrap, and impact-absorbing foams are installed. Subsequently, they are placed inside 5-layer cardboard boxes and finally wrapped in shrink wrap.
9. Storage and Shipping
Each packaged component is placed in a designated section of the warehouse according to the scheduled shipping plan. Subsequently, under the supervision of the quality control unit and in coordination with the esteemed sales representatives, the loading process is carried out, and the products are dispatched to all parts of the country.
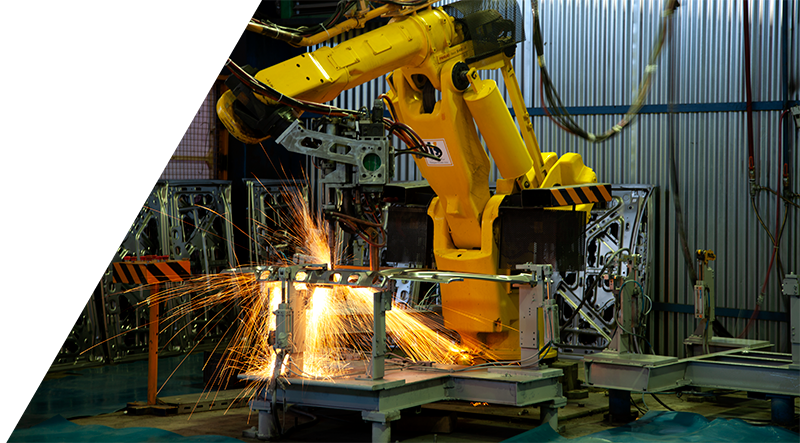
Assembly
The produced Parts
The products of this company are divided into two main categories: those used in the production lines of the country’s automotive industry and those used in the market for spare parts. We take pride in being the provider of the most comprehensive and highest-quality range of metal body products for passenger cars in the country. The company’s products are categorized into three groups for the vehicles of Iran Khodro, SAIPA, and Renault Pars, and the diversity of these items includes the following car models:
Peugeot 405, Peugeot SLX, Peugeot Pars, Peugeot 206, Samand, Arisan, Pride Saba, Pride 132, Tiba, Tondar 90, and Dena.
Raw materials
The quality and suitability of raw materials are essential elements of high-quality and premium production. The raw materials used in the production lines of Asia Khodro Synchronization Company include various types of sheet metal, primer paint, cardboard, shrink wrap, etc. All these materials are selected from among the top domestic manufacturers based on the latest industry standards by experienced experts in the procurement and quality control unit of Asia Khodro Synchronization Company.
Production Mechanism
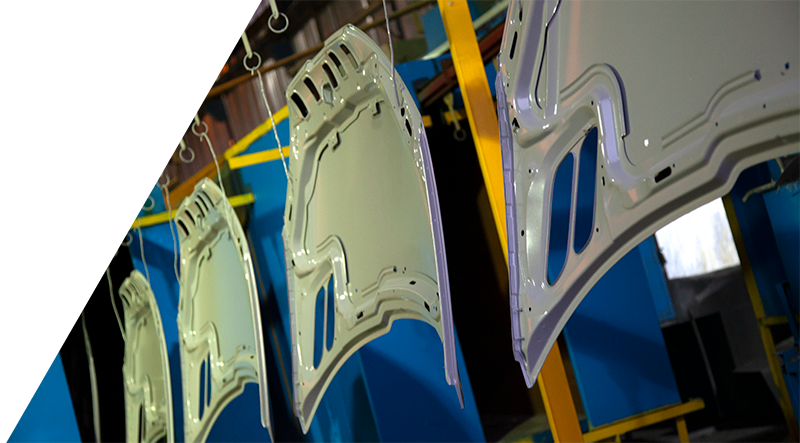
Color
Introduction to Painting Lines
• Equipped with three separate semi-automatic lines for liquid and powder (electrostatic) paint spraying, along with washing and degreasing using reputable materials supplied by standard-compliant companies recognized by domestic automakers.
• The primer paint used in Asia Khodro Synchronization Company is of the highest quality, containing corrosion-resistant zinc phosphate pigments. It exhibits high resistance to moisture, oil-based solvents, and mineral oils, and is sourced from reputable automotive paint factories with industry standards.
• The laboratory is equipped with various industrial paint testing devices, such as cross-cut, bending, salt spray, impact testing, etc.
• Waxing of components for filling gaps and sealing the edges of assembled hemmed parts, using waxes commonly used in the production lines of domestic automakers.
• Quality control stations in the paint halls for controlling the input of raw materials and 100% inspection of the produced products, accompanied by the installation of quality labels on all components.
• Packaging of products with 3-layer and 5-layer cardboard boxes, along with impact-resistant foam, bubble wrap, and shrink wrap for protecting components against dust, moisture, and impact.
Latest News